Understanding Plastic Mold Manufacturing
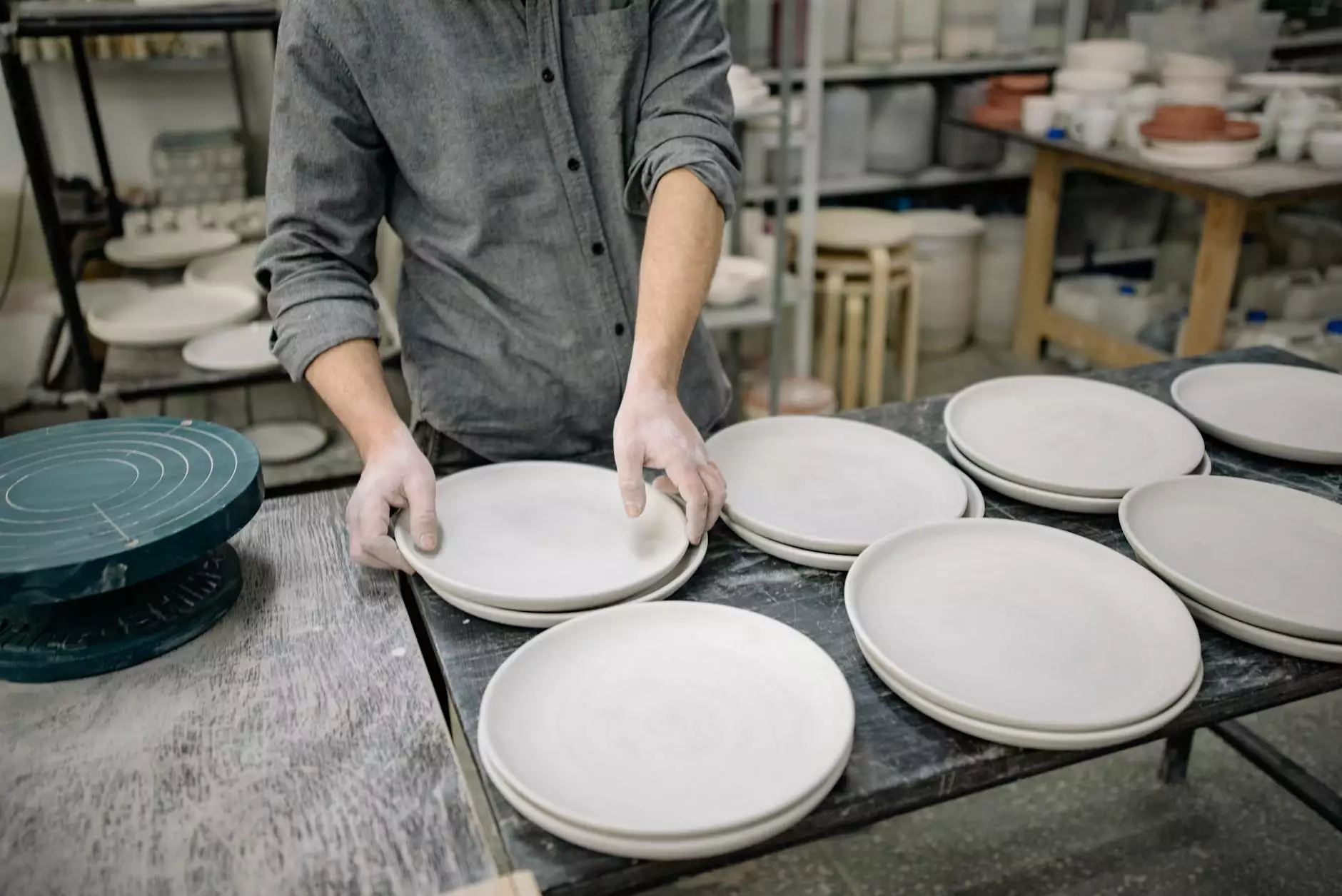
The world of manufacturing is continually evolving, and at the heart of many innovative products is plastic mold manufacturing. This process involves creating molds that can produce high-quality plastic parts, essential for numerous industries, including automotive, consumer products, and electronics. In this article, we will delve into the fascinating world of plastic mold manufacturing, exploring its processes, benefits, and applications.
What is Plastic Mold Manufacturing?
Plastic mold manufacturing is a process that involves designing and producing molds used to shape plastic materials into specific configurations. The process typically involves several stages, including:
- Designing the Mold: This initial step requires careful consideration of dimensions, materials, and the intended use of the final product.
- Machining the Mold: Once designed, a mold is machined with precision to create the exact specifications required.
- Injection Molding: The final step where plastic is injected into the mold to create the finished product.
The Importance of Plastic Mold Manufacturing
In today's manufacturing landscape, the importance of plastic mold manufacturing cannot be overstated. Here are some key reasons why:
- Efficiency: Mold manufacturing allows for high production rates, minimizing waste and maximizing efficiency.
- Cost-Effectiveness: Mass production through molds significantly lowers the cost per unit, making it an economical choice for manufacturers.
- Versatility: Molds can be used to produce a vast array of products in various sizes and shapes, offering manufacturers flexibility.
Types of Molds in Plastic Mold Manufacturing
There are several types of molds used in plastic mold manufacturing. Understanding these can help businesses choose the right type for their needs:
- Single Cavity Molds: In these molds, a single product is formed at a time. They offer high accuracy and are ideal for smaller production runs.
- Multi-Cavity Molds: These molds can produce multiple identical parts at once, significantly increasing production efficiency.
- Family Molds: Used to produce different parts that share the same base design, family molds are useful for creating product lines with similar features.
- Stack Molds: Utilizing multiple plates, they allow for simultaneous production on both sides of a mold, doubling output without increasing floor space.
The Process of Plastic Mold Manufacturing
1. Designing the Mold
The design phase of plastic mold manufacturing is critical. Utilizing CAD (Computer-Aided Design) software, engineers create detailed models that specify every dimension and feature of the mold. Factors such as shrinkage, draft angles, and tolerance levels are carefully calculated to ensure the end product meets exact specifications.
2. Selecting Materials
Choosing the right materials for mold construction is vital. Common materials include:
- Steel: Often used for its durability and ability to withstand high pressures, steel molds are suited for long production runs.
- Aluminum: Lighter and less expensive, aluminum molds are ideal for short runs and prototypes.
- Composites: For specific applications, composite materials can offer unique properties such as chemical resistance.
3. Machining the Mold
The machining process involves using advanced tools and techniques to create the mold parts. CNC (Computer Numerical Control) machines provide precision and efficiency, producing intricate designs that manual machining cannot achieve.
4. Assembly and Testing
Once all mold components are machined, they are assembled. This phase often includes extensive testing to ensure that mold cavities are uniform and that parts can be ejected easily after molding.
5. Injection Molding Process
The injection molding phase is where the actual plastic mold manufacturing occurs. Plastic resin is melted and injected into the mold under high pressure. The material cools and solidifies, taking on the mold’s shape, and is then ejected, creating high-quality plastic parts.
Applications of Plastic Mold Manufacturing
The versatility of plastic mold manufacturing allows its application across various industries:
- Automotive Industry: Components such as dashboards, bumpers, and housing are often produced using plastic molds.
- Consumer Products: Everyday items such as containers, toys, and appliances are created through this process.
- Medical Devices: Precision and reliability in mold manufacturing ensure that medical equipment meets stringent health standards.
- Electronics: Molds produce housings, bezels, and various casing components in electronics.
Benefits of Plastic Mold Manufacturing
Adopting plastic mold manufacturing offers numerous advantages for businesses:
- Scalability: Businesses can easily scale production volumes up or down based on market demands.
- Reduced Waste: The precision of mold design minimizes excess plastic waste, making it an environmentally friendly option.
- Durability and Strength: Products made from plastic molds are often robust and can withstand various stresses.
Innovations in Plastic Mold Manufacturing
Technology is making significant strides in plastic mold manufacturing:
- 3D Printing: Rapid prototyping through 3D printing allows for faster mold design and testing.
- Smart Manufacturing: The introduction of IoT in manufacturing helps in monitoring processes and improves efficiency.
- Advanced Materials: Research into new composite materials is expanding the capabilities of plastic molds.
The Future of Plastic Mold Manufacturing
The future of plastic mold manufacturing looks promising. As industries continue to innovate, the demand for high-quality, reliable, and efficient mold manufacturing will only increase. Businesses that adopt the latest technologies and practices will be better positioned to compete in the global market.
Conclusion
In conclusion, plastic mold manufacturing is an integral part of modern industrial production, providing efficiency, versatility, and cost-effectiveness. Understanding its processes, benefits, and applications allows businesses to harness the full potential of this manufacturing method, enabling them to bring innovative products to market. By partnering with experts in the field, such as those at deepmould.net, manufacturers can ensure high-quality outcomes tailored to their specific needs.
For more information about plastic mold manufacturing and its benefits, visit deepmould.net.