Understanding Injection Mold Plastic: A Comprehensive Guide
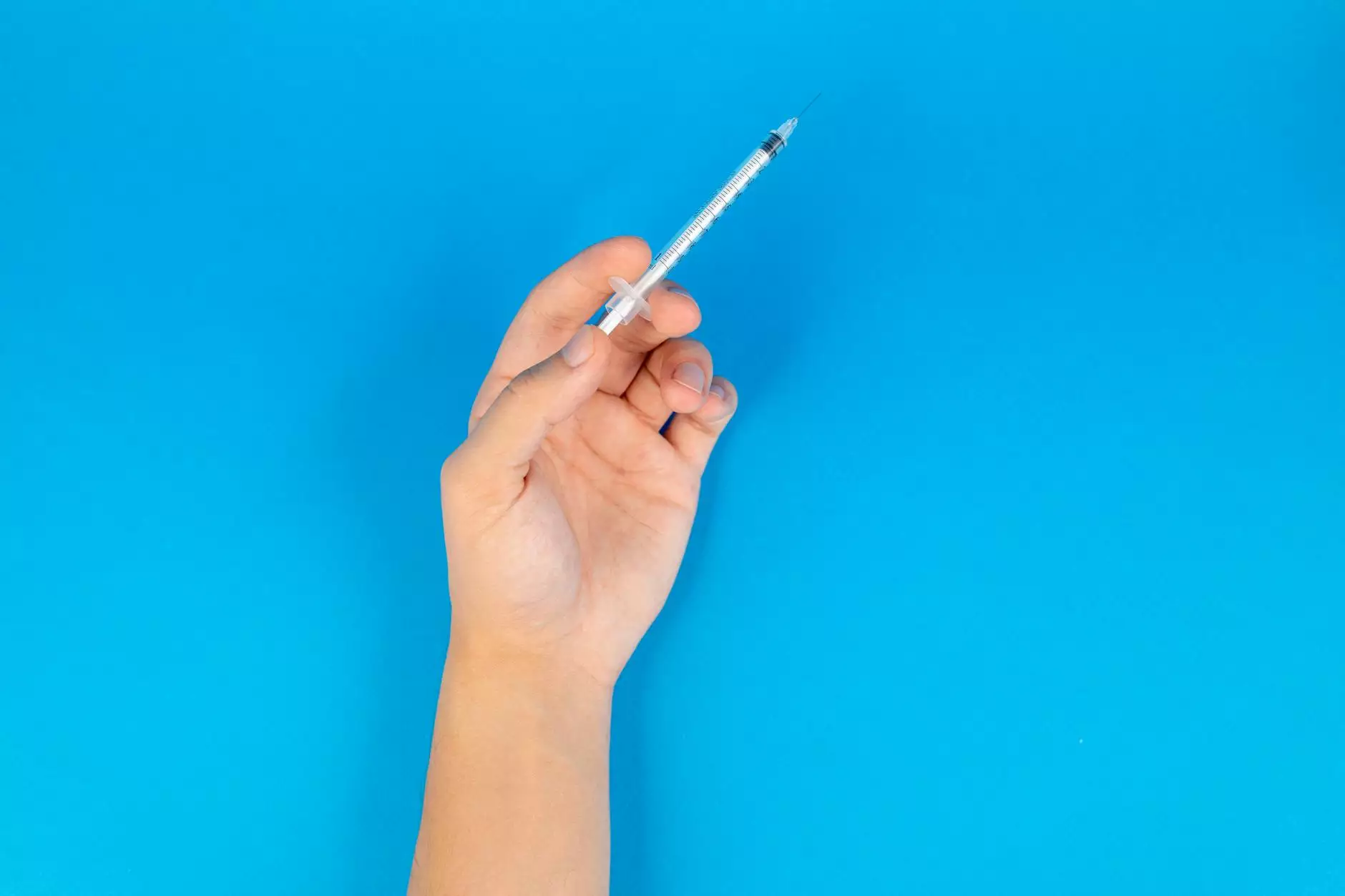
Injection mold plastic has become an integral part of the manufacturing landscape, offering unmatched efficiency, precision, and versatility. In this extensive article, we will delve deep into the intricacies of injection molding, explore its applications, advantages, and why it stands out in the world of materials and production methods. Whether you are in the business of metal fabrication or simply keen on understanding modern manufacturing techniques, this guide is tailored to provide you with all the essential knowledge.
What is Injection Molding?
Injection molding is a manufacturing process for producing parts by injecting molten material into a mold. It’s primarily used in the plastic industry but is also applicable to metals and other materials. The process involves the following steps:
- Material Feeding: The raw material, usually in the form of pellets, is fed into the injection molding machine.
- Melting: The pellets are heated until they melt into a viscous liquid.
- Molding: The molten material is injected into a mold at high pressure.
- Cooling: The material is allowed to cool and solidify within the mold.
- Demolding: Once solidified, the mold opens, and the finished product is ejected.
Types of Injection Mold Plastics
There are several types of plastics commonly used in injection molding, each with unique properties suited for various applications. Here are some of the most widely used:
- Polypropylene (PP): Known for its chemical resistance and low density, making it ideal for packaging and automotive components.
- Polyethylene (PE): Highly versatile, available in various densities, and used extensively in bags and containers.
- Polyvinyl Chloride (PVC): Known for its durability and rigidity, widely used in pipe and fittings.
- Acrylonitrile Butadiene Styrene (ABS): Offers excellent strength and toughness, commonly used in electronics and automotive parts.
- Polystyrene (PS): Commonly used in disposable cutlery and containers due to its rigidity and ease of production.
The Advantages of Using Injection Mold Plastic
The appeal of using injection mold plastic lies in its numerous advantages:
1. Efficiency in Production
Injection molding allows for the production of large quantities of parts with minimal waste. Once the mold is created, it can be used repeatedly, ensuring high efficiency and low per-unit costs.
2. Precision and Accuracy
The injection molding process is highly precise, allowing manufacturers to produce complex shapes and designs that meet tight tolerances. This is particularly crucial in industries such as automotive and aerospace where failure to meet specifications can be costly.
3. Design Flexibility
Injection molds can be designed to create intricate patterns and specifics. This flexibility enables designers to innovate and experiment with different shapes, sizes, and functionalities of products without substantial increases in production costs.
4. Variety of Materials
The process accommodates a wide range of materials. From thermoplastics to thermosetting plastics, the choice of material can be tailored to the specific needs of the application, ensuring optimal performance.
5. Reduction of Waste
Injection molding is a sustainable process that minimizes waste. The only waste produced is typically the sprue or runner system, which can often be recycled. This is an environmentally friendly advantage that many businesses prioritize.
Applications of Injection Mold Plastic
Injection molding is a versatile process that serves various industries. Here are some key applications:
1. Automotive Industry
The automotive industry extensively uses injection mold plastic for manufacturing components such as dashboards, door panels, and the interior linings of vehicles due to the materials' durability and lightweight properties.
2. Consumer Goods
Household items such as storage containers, toys, and kitchen utensils are commonly produced using injection molding, as the process allows for high-volume production at reasonable costs.
3. Electrical and Electronics
Injection molding produces various electric casing and components, ensuring they meet rigorous safety and performance standards while maintaining tight tolerances.
4. Medical Devices
In the medical field, precision is crucial. Injection molding allows for the production of intricate instruments and devices that meet stringent regulations.
5. Packaging
Many types of packaging, including bottle caps and containers, are created through injection molding, utilizing the speed of production and material versatility.
Steps to Initiate the Injection Molding Process
If you’re considering utilizing injection mold plastic for your manufacturing needs, here are steps to help you get started:
1. Design and Prototyping
Before anything else, a detailed design must be created, ideally using CAD software. This will include a prototype to test the design's functionality and performance.
2. Mold Design
The mold itself must be designed, which involves selecting the right materials and specifications. This step often requires collaboration with mold makers to optimize the design for production efficiency.
3. Material Selection
Select the right plastic type based on the desired properties, such as strength, flexibility, and chemical resistance.
4. Production Planning
Create a production plan that includes timelines, cost estimates, and quality checks throughout the process.
5. Launching Production
Once everything is in place, production can commence, with continuous monitoring to ensure quality standards are met.
Key Considerations for Successful Injection Molding
To ensure success in injection molding, consider the following:
1. High-Quality Molds
Investing in high-quality molds can reduce production costs over time due to their durability and efficiency.
2. Understanding Material Properties
Diving deep into the properties of the plastic chosen for the job can make a significant difference in product performance and longevity.
3. Continuous Improvement
Regularly evaluate the production process and implement improvements based on recent advancements in technology and material sciences.
The Future of Injection Mold Plastic
The future for injection mold plastic appears bright, driven by technological advancements such as:
1. Increased Automation
Advancements in automation will lead to faster production cycles and reduced labor costs, making injection molding even more efficient.
2. Sustainable Practices
New innovations are emerging to recycle plastics and reduce waste further, aligning with global sustainability goals.
3. Advanced Materials
Developments in materials science continue to enhance the performance characteristics of injection mold plastics, creating options that withstand extreme conditions.
Conclusion
In summary, injection mold plastic serves as a cornerstone of modern manufacturing. Its myriad applications, efficiency in production, and precision make it invaluable across various industries. By understanding the dynamics of injection molding, businesses can not only optimize their production processes but also innovate new designs that meet the ever-evolving needs of consumers. Whether in automotive, electronics, or consumer goods, the impact of injection molding will continue to be significant in shaping the future of manufacturing.
As companies look to the future, embracing the benefits of injection molding and the flexibility of various plastic materials will be crucial. For more information on how deepmould.net can assist with your injection molding needs, contact us today and unlock the potential of this revolutionary manufacturing process.